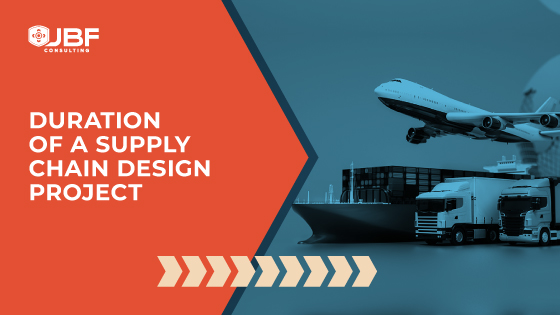
The duration of a Supply Chain Design (SCD) project, also called Network Design and Network Optimization, is dependent on many factors including availability of data, quality of data, the ability of the analysts/modelers, and level of detail desired.
In our experience, a project that we would consider “investment grade” which includes inbound and outbound transportation costs, warehousing costs and inventory costs typically requires 12 to 14 weeks to complete.
We’ve seen some completed in 10 weeks while others as much as 16 weeks or even more if the work is being conducted in-house on a part-time basis. This range has been confirmed by many of our colleagues in the business.
A Sequential Order
There is also a particular order to an SCD project and skipping steps often ends up in more work down the road with delayed results instead of a shortened timeline.
For instance, when pressed for time, moving ahead with an incompletely cleaned dataset has caused me to scrap and restart my model in more instances than once after significant holes were found in the data.
Of course, there is a certain amount of art to the modeling and knowing when to proceed is a skill an analyst needs to develop.
Don’t let perfect be the enemy of good as they say!
Team Size
With SCD being mostly a sequential, linear process, there is a limited amount of work that can be conducted in parallel. The point being that throwing more resources at a project beyond a certain limited level will not appreciably shorten the timeline.
You can’t get a good omelet by doubling the heat and halving the cooking time.
Typically, an SCD team is one to four full-time equivalents. The optimal size of the team being mostly dependent on the quantity and quality of input data streams and consequently set at the start of the project. A 5-person team is perhaps as big a team we’ve seen work on a single SCD project. This was for a big study involving more than 9 business units with as many data sources (ERPs, TMSs, and WMSs).
Once a model is built, the team can shrink to one or two people to run the what-if analysis and interpret the results.
Project Scope
Considering the nature of SCD projects where there is limited benefit to increasing resources as discussed above, in cases where the timeline is fixed and does not allow for the required 12 to 14 weeks, the only available option is to reduce the scope of the project.
There are many ways to reduce the scope of an SCD project.
One approach may be to limit the number of scenarios to investigate. Another may be to limit the geographies such as including only the US vs. all of North America.
In our experience, the path most often taken is to limit the scope of the category of data going into the model.
For instance, an analyst may decide to skip including warehousing and inventory costing in his model in order to meet a tight deadline. Under even tighter time constraints, inbound transportation cost modeling may be entirely skipped or a single average value (i.e., one cost per unit of distance and weight) may be used for transportation costs.
Model Precision
Unfortunately, this latter type of scope reduction also results in a reduction in model precision and costly decisions are often made without consideration for this flaw.
Reasons For This Situation
The first is the strategic/long-term nature of the decision being made. Opening a new DC takes months if not years. By the time the change is made, and operations settle down, there is little interest in going back to validate the results of the SCD project. Thus, there is no feedback loop and any oversimplifications or errors may be perpetuated with subsequent studies.
The second reason has to do with the poor understanding behind the concepts of SCD often resulting in the belief that any result is better than no result. At its core SCD is mathematical optimization in the form of mixed-integer programming.
Yes, somewhat of a mouthful and not easily grasped by a casual observer. The human brain is known to have problems understanding the inter-related correlation between 4 variables let alone the thousands involved in SCD.
In an overly simplified model, results often echo the intuitive hypothesis and decision-makers fall prey to confirmation bias. Experience has shown me that fully developed models often provide counterintuitive results.
An example of this situation was a model we built using only outbound transportation data. Results indicated that Columbus, OH would be a good location to fulfill orders for the greater Northeast area thus confirming the hunch of the Transportation Director.
However, once the inbound transportation data was included in the model, the best location shifted to Indianapolis, IN due to a preponderance of suppliers in the Midwest and West Coast.
Overall, the difference represented $1.5M in yearly savings and well worth the additional work to include the data in the model.
Sensitivity Analysis
Conducting a sensitivity analysis is a good way to establish the precision of a result for a given model. However, such an analysis still suffers from the inherent limited precision of the model.
A location 100 miles apart from another may represent limited savings in transportation costs alone in a simplified model, but may be much more expensive to operate once labor and real estate costs are factored in.
Conclusion
To conclude, it is possible to run SCD studies in a matter of a few weeks or even days. The compromise is in the precision of the results. Due to the nature of the analysis it is hard to ascertain the precision of these findings.
If you want to provide investment grade results, budget 12 to 14 weeks of time for a team of 1 to 4 players depending on the amount of data that is to be considered by the model.
Next Steps
Do you have the right footprint for your network?
Are you looking to reduce costs?
Please reach out to us for more information.
Founded in 2003, JBF Consulting is a supply chain execution strategy and systems integrator to logistics-intensive companies of every size and any industry. Our background and deep experience in the field of packaged logistics technology implementation positions us as industry leaders whose craftsmanship exceeds our client expectations. We expedite the transformation of supply chains through logistics & technology strategy, packaged & bespoke software implementation, and analytics & optimization. For more information, visit us at www.jbf-consulting.com